Health and Safety
Health Management
In June 2017, the Teijin Group announced the Teijin Group Health Management Declaration, demonstrating its commitment to actively promoting the mental and physical health of its employees, who it views as the ultimate management resource. In accordance with this declaration, we are working to create vibrant workplaces that offer peace of mind to our employees so that we can achieve sustainable growth as a company. As part of our health management efforts, we compile and distribute the Health Management Handbook as an opportunity for each of our employees to contemplate their own health as an important issue. Guided by our desire to remain a company that respects the health of its employees, we will continue to roll out a wide variety of activities while collaborating with each Group company.
- *The Teijin Group was recognized as a Certified Health and Productivity Management Organization by the Ministry of Economy, Trade and Industry for its excellent health management. We have received this recognition for eight consecutive years.
The Teijin Group health management declaration
The Teijin Group believes that employees are the ultimate management resource. We are committed to promoting the development of employees who are full of vigor and to the creation of vibrant workplaces for the sustainable growth of the company, and will continue to actively promote the mental and physical health of our employees. At the same time, the Teijin Group strives to contribute to the health of people around the world and improve quality of life through its business activities.
(Established on June 16, 2017)
Health Management Policy
The Teijin Group is strategically involved in the health management of its employees based on its Corporate Philosophy.
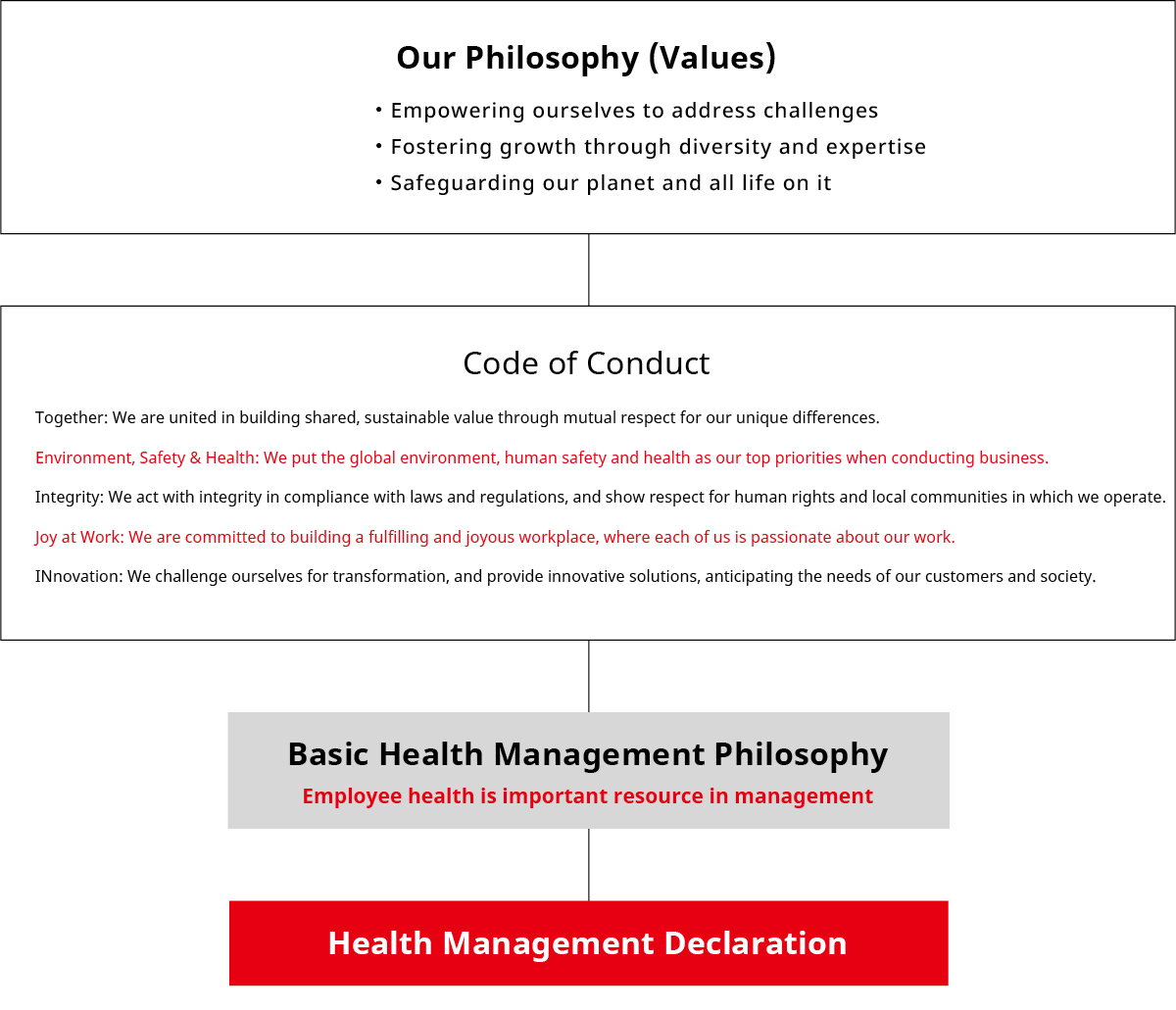
System for Promoting Health Management and Future Direction
The Health Care Administration Office is positioned as a promotion department, and health management is promoted in cooperation with the Teijin Group Health Insurance Association, industrial physicians, and occupational health staff under the direction of top management.
Organization Chart of the Promotion System
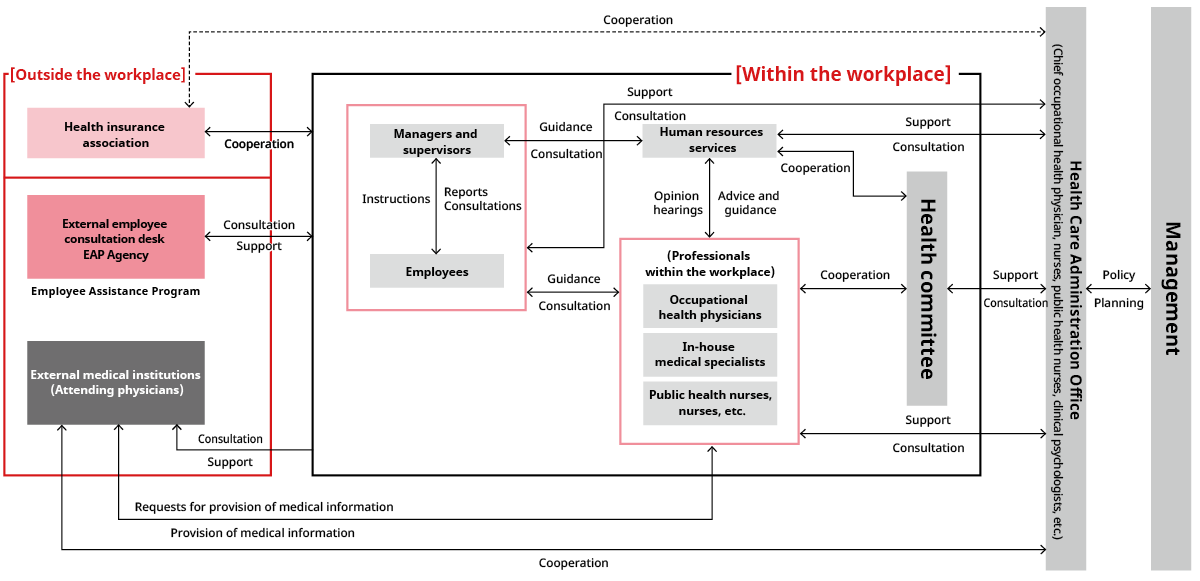
Future Direction (medium-term issues)
By visualizing the results of the health management initiatives that we have been implementing to improve the well-being of our employees, we will enhance employee work engagement and foster a corporate culture that better facilitates innovation.
Mental Healthcare Measures through Close Cooperation

In regard to mental health, Teijin has established consultation services for employees both within and outside the Company and the Health Care Administration Office provides tailored mental support under the guidance of medical specialists. In FY2023, staff of the Health Care Administration Office (clinical psychologists, health nurses, nurses) and the external Employee Assistance Program (EAP) received a total of 2,026 consultations including online and telephone consultations. Preventive education for mental health is also carried out periodically by staff at the Health Care Administration Office, such as new employee self-care seminars and line-care seminars. In all, 43 sessions were held in FY2023, attended by approximately 1,700 individuals.
Implementation of a Diagnosis to Measure the "iki-iki" Level of Individuals and Workplaces
The Teijin Group has been diagnosing stress levels in all workplaces in Japan every year since 2003. Furthermore, in line with stress check legislation, in July 2016 it implemented the annual initiative of a diagnosis to measure the iki-iki (cheerfulness) level of individuals and workplaces. This diagnosis combines the workplace stress diagnosis with a stress diagnosis for individuals. Those workplaces diagnosed as exceeding a certain level were the focus of workplace improvement activities to achieve bottom-up improvement through discussions with employees in the field. The results of the June 2023 diagnosis (an effectiveness measurement) showed that these activities had led to improvements in approximately 87% of the workplaces concerned. Furthermore, from FY2019, we have been conducting "briefings on how to view the results of diagnosis to measure the iki-iki (cheerfulness) level of workplaces" targeting managers and encourage each department to improve the understanding of the results of group analysis and the methods of utilizing it, and are working on promoting activities to improve the workplace environment. Teijin will continue aiming to create cheerful and comfortable workplaces through these diagnosis and improvement activities.
Prevention and Health Promotion Measures for Health in Collaboration with Health Insurance Providers
The Teijin Group is collaborating with health insurance providers to implement a data health plan (Colla-Health) based on analysis of health data. This involves utilizing the data of individual employees held by our company and health insurance providers to roll out health insurance business narrowing down the target by risk type and deploying various health insurance businesses ranging from popular approach (approaching a particular group overall) to severe illness prevention.
ESH Management Activities
The Teijin Group positions Environment, Safety and disaster prevention, and Health (ESH) as key initiatives in all business activities and promotes ESH management across the entire group.
Goals and Basic Policies on ESH
In addition to compliance with the domestic and foreign relevant laws and municipal ordinances, we set forth our self-imposed goals for ESH management and its basic policies as follows.
Goals for ESH management
In accordance with the Teijin Group's ultimate goals -- the Challenge "ZERO," the goals for ESH management in business activities shall be the following four items:
- 1.Environmental conservation Zero environmental problems
- 2.Safety Zero labor accidents
- 3.Disaster prevention Zero explosions and fires
- 4.Health Zero occupational diseases
Teijin Group ESH Basic Policies
- 1.We make safety our highest priority, following our philosophy of protecting human life.
- 2.ESH is the responsibility of every production line manager.
- 3.ESH efforts are integral to every stage of business activities.
Group ESH Management System
The Teijin Group established the Group ESH Subcommittee under the Group CSR Committee to practice integrated environment, safety, and health (ESH) management. The Group ESH Subcommittee holds regular meetings twice a year to deliberate on policy, measures, and activities regarding ESH management, which are then expanded within the Group. The ESH Committee members appointed for each business unit serve as chairpersons of the ESH Committee and promote ESH management for each business. Every year, the Teijin Group holds the Group CSR Committee, where Groupwide ESH results and activities status are reported. Additionally, the Teijin Group shall lay down criteria for the establishment of the ESH Management System (ESH-MS) at each factory and other facilities, as outlined in the "Standards for the Establishment of the Group's ESH Management System."
Objectives to establish the ESH Management System (ESH-MS)
- 1.Each factory and other facilities will secure their ESH management at a certain level and continuously improve their ESH performance by establishing and appropriately implementing the ESH-MS.
- 2.Through the establishment of the ESH-MS based on the international common standards such as ISO 14001 and ISO 45001, the Teijin Group will objectively show its stakeholders (shareholders, customers, business partners, regional society, and administrative organizations, etc.) that it maintains the level of its ESH management above the average.
- 3.Through the construction and operation of international common standards or ESH-MS based on those common standards, the Teijin Group will share the "common ideology and language of the ESH Management" among all factories, etc.
ESH assessment and auditing
Through the ESH assessment system, Teijin reviews and verifies the related laws and regulations together with the ESH risk related to project implementation and day-to-day matters, and endeavors to implement appropriate measures in line with compliance and risk. We also conduct ESH Audit A and ESH Audit B in accordance with our ESH Audit Regulations, forming a double audit system. Audit A is conducted by the Chairperson of the ESH Committee for each business unit. and Audit B is conducted by the general manager of the Environment and Safety Department, who has been instructed by the Chief Production, Engineering & Procurement Officer. As part of the audit process, each business unit reports on ESH management status, any accidents, the status of countermeasures, and the status of ESH activities. This content is then audited, and confirmation and guidance are provided in relation to future issues and actions required before the next audit.
Outline of the audits | Auditors | FY2023 audit results | |
---|---|---|---|
ESH Audit A | ESH audits at production sites | Chairperson of Business Unit ESH Committee | 23 bases (15 within Japan, 8 overseas) |
ESH Audit B | Audits of the results of each business unit's ESH Audits | General Manager of the Environment and Safety Department | 16 cases (2 composites factories, 9 business units, 5 directly managed companies) |
ESH education
The Group ESH Educational Workshop designed to enhance the level of ESH management is held once per annum. The workshop targets the ESH staff of business units and Group companies as well as production line managers, Group company presidents, and factory managers. In FY2023, we postponed the workshop in consideration of the COVID-19 pandemic.
Training for internal auditors of ESH compliance
To enhance compliance with laws and regulations related to ESH, every year we hold a course to train Group employees as internal auditors for ESH compliance. In FY2023, 83 employees were newly certified as Grade 1 internal auditors for ESH compliance and 24 employees were certified as Grade 2 internal auditors for ESH compliance.
Responding to an ESH accident
In preparation for the occurrence of an ESH-related accident, the Teijin Group defines and enforces rules about swiftly reporting any incidents to the responsible persons within the Group.
Prioritization and Action Plans in FY2024
In FY2024, we will address the following priority issues with the aim of achieving zero ESH accidents in our business activities.
- 1.Further reduce occupational accidents and disaster prevention incidents, and eliminate serious accidents.
- 2.Suppression of work and behavior-related accidents.
- 3.Review and promotion of disaster prevention management.
- 4.Compliance with environmental regulations and strengthening of chemical substance management.
Security and Disaster Prevention Activities
System to Promote Disaster Prevention Management
The Teijin Group is engaged in disaster prevention management and has established Groupwide disaster prevention guidelines. For each fiscal year, we design plans based on these guidelines relating to preventative measures, such as disaster prevention assessment, fire prevention, and earthquake countermeasures, as well as planning and implementing initiatives including the strengthening of disaster prevention training and drills and upgrading of fire prevention equipment. Each business unit/manufacturing site manages the implementation status and achievements of these disaster prevention activities and gives guidance to improve any areas of noncompliance. The results of this are then audited by the Chief Sustainability Officer at the end of each fiscal year.
Implementing Disaster Prevention Assessments
The Teijin Group has been conducting disaster prevention diagnoses since 1980 and mini disaster prevention diagnoses since 2008 in line with its own independent standards. In Teijin's aramid business, process safety management (PSM) has been introduced at Teijin Aramid B.V. affiliated chemical plants in the Netherlands, Japan, and Asia. Disaster prevention diagnoses and PSM are used to assess safety every five years by experts in manufacturing, facilities, and ESH at a total of 15 plants globally. These are Teijin Group plants where large amounts of hazardous substances are handled. Mini disaster prevention diagnoses mainly examine fire prevention, focusing on small-scale locations with a risk of fires, such as boilers and places where hazardous materials and combustibles are stored (25 factories). We conduct an examination every five years. In FY2023, we carried out diagnoses at 18 risk areas in 12 factories.
Trends in the number of disaster prevention-assessed plants
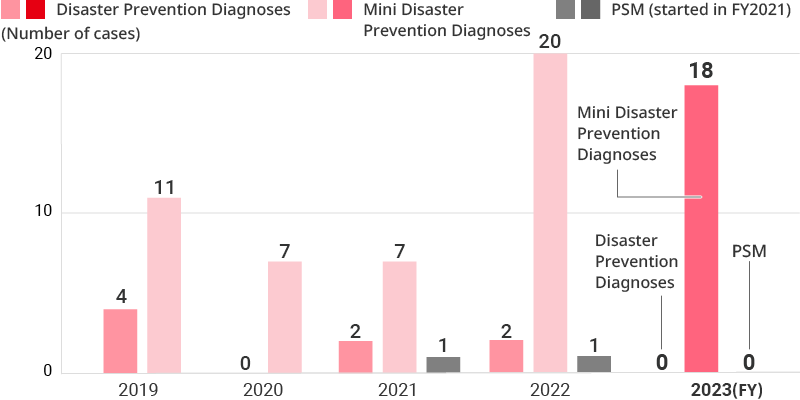
Other Activities Aimed at Realizing Zero Serious Accidents
To achieve our aim of realizing zero "serious accidents," which we have defined as including explosions, fires, and external leakage/spills of hazardous substances, we are taking various measures to reinforce disaster prevention including disaster prevention diagnoses, training, and drills at our chemical plants and power plants. In December 2022, there was a fire at the Delfzijl Plant of Teijin Aramid. After this incident, in FY2023 we launched a countermeasure program under which we have continued to engage in activities to ascertain the causes of the fire and prevent a reoccurrence.
Trends in the number of serious accidents and disaster
We are continuously taking various measures to reinforce disaster prevention, including disaster prevention diagnoses, training, and drills.
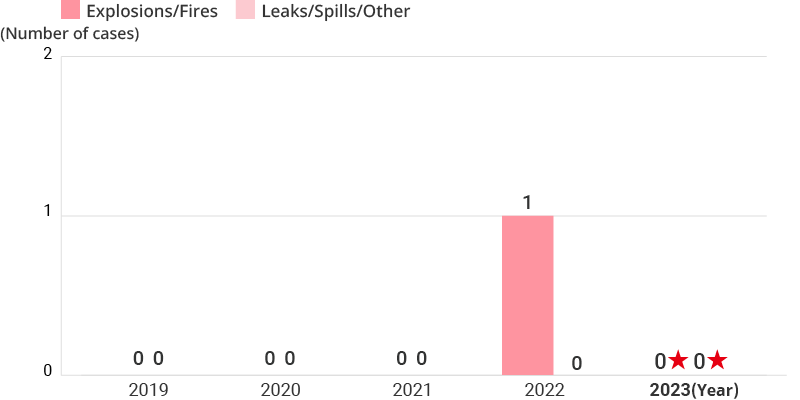
- *A serious accident refers to explosions or fire accidents, accidents involving leakage or outflow of hazardous materials or hazardous substances, which have caused human damage (lost-time injury accidents), or have affected the local community, or have involved full-scale external support.
- *Figures are calculated based on calendar years
Fire Prevention Activities
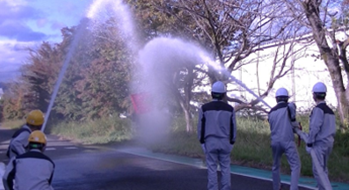
Since 2008, November 10 has been the Teijin Group Fire Prevention Day. On this day, each Group company conducts its own fire prevention activities, as well as common activities for the whole Teijin Group, such as periodical fire prevention checks. These activities are shared Groupwide in order to strengthen the fire prevention system.
Disaster Prevention Training (Evacuation Drills)
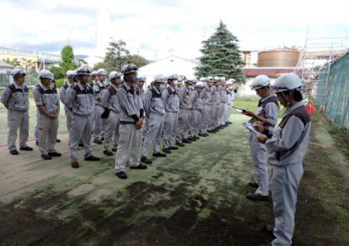
Since the Great East Japan Earthquake struck on March 11, 2011, the Teijin Group has continued to implement evacuation drills assuming the occurrence of a natural disaster. After the drills, we hold review meetings and endeavor to improve our antiearthquake manual. Training was carried out at plants and facilities in Japan in FY2023 as well (including tabletop exercises).
Occupational Safety Activities
Occupational safety promotion system
To reduce risk in the workplace, the Teijin Group encourages its manufacturing and processing sites to obtain occupational health and safety management system certification (ISO 45001 and Standardization of Safety Production). As of the end of March 2024, a total of 40 business sites and plants have acquired the occupational health and safety management system certification.
Current status of OHSAS management system certification
Japan (12 companies, 18 factories)
Teijin | Iwakuni, Matsuyama, Mishima, Ibigawa, Mihara | Teijin Frontier | Matsuyama, Ibigawa |
Unisel | Iwakuni |
Teijin Tedy | Matsuyama |
Hiroshima Plastic | Hiroshima |
Teijin Eco-Science | Matsuyama |
Teijin Pharma | Iwakuni |
Teijin Kosan | Ehime | Toho Chemical Engineering & Construction | Mishima, Tokushima |
Toho Machinery | Tokushima |
Infocom West Japan | Matsuyama |
Teijin Regenet | Iwakuni |
Overseas (16 companies, 22 factories)
The Netherlands | Teijin Aramid | Delfzijl、Arnhem、Emmen |
---|---|---|
China | Teijin Chemicals Plastic Compounds (Shanghai) | Shanghai |
Teijin Polycarbonate China | Zhejiang | |
Nantong Teijin* | Nantong | |
N.I. Teijin Airbag Fabric*(Nantong) | Nantong | |
Teijin Automotive Fabrics Finishing*(Nantong) | Nantong | |
Teijin Product Development China* | Nantong | |
Thailand | Teijin Corporation (Thailand) | Ayutthaya |
Thai Namsiri Intertex | Weaving:Chacheongsao、Dyeing:Samutprakarn | |
Teijin (Thailand) | Ayutthaya | |
Teijin Polyester (Thailand) | Pathumthani | |
Teijin Cord (Thailand) | Ayutthaya | |
Germany | Teijin Carbon Europe | Heinsberg |
Spain | Esteve Teijin Healthcare S.L. | Castelldefels |
Portugal | Teijin Automotive Technologies Portugal | Leça do Balio、Palmela |
Czech Republic | Teijin Automotive Technologies Czech | Čejetice、Čejetičky、Milovice |
- *Standardization of Safety Production
Occupational Safety Promotion Activities
Promoting the three pillars of safety activities
In order to prevent occupational accidents, the Teijin Group has established three pillars of safety activities: the "5S" initiative (referring to the five Japanese words seiri, seiton, seiso, seiketsu, and shitsuke, which correspond to organization, tidiness, cleaning, hygiene, and discipline); the "Hiyari" or "Hatto" (meaning close call or near miss) initiative; and safety patrols. These activities from Japan are expanded as activities common to the Teijin Group including overseas Group companies. Utilizing the information obtained through these activities, we aim to enhance individual awareness of risks and communication in the workplace in order to eliminate occupational accidents within the Teijin Group.
In addition, we hold monthly safety and health committee meetings at each location, bringing together worker representatives, company representatives, and industrial physicians as a forum for sharing information and holding discussions. Furthermore, we share information and hold discussions through our own activities, such as the ESH Promotion Committee, to ensure workplace safety and to raise the level of our safety activities.
Initiatives aimed at preventing lost-time injuries
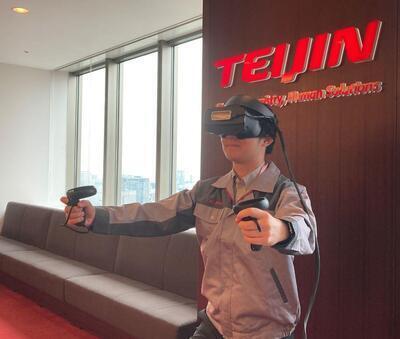
In FY2023 (April 2023 through March 2024), there were six lost-time injury accidents related to rotors. Prevention of entanglement in rotors (rotor-related accidents), which can cause serious injury, is addressed as a priority issue. In FY2023, we held a rotating machinery accident response meeting with relevant business units and have been conducting activities on an ongoing basis to eliminate accidents involving rotating machinery within the Teijin Group. In FY2024, with the aim of minimizing the occurrence of accidents caused by work or conduct, which have accounted for the majority of lost-time injury accidents, countermeasures utilizing virtual reality (VR) technology to raise hazard perception and enhance sensitivity to danger will be taken, along with awareness-building efforts to achieve safe behaviors based on the behavior-based safety (BBS) process. At the same time, we are focusing on measures targeting inexperienced workers with limited field experience, in particular, and roll out relevant measures in our overseas businesses. Moreover, the Teijin Group receives and assesses reports on lost-time accidents of subcontracting companies that occur at Group business sites and supports/promotes initiatives by subcontracting companies to secure safety.
Groupwide sharing of occupational accident information and responses at the time of an accident
Information relating to all occupational accidents resulting in lost time due to injury that occur at Teijin Group companies is distributed via an intranet to enable these experiences to be used as a reference and to help prevent the recurrence of similar accidents. In particular, if the circumstances and cause of the accident satisfy the requirements for a special audit as described in the ESH Audit Regulations, a special audit is performed either by the head office or the relevant business unit, depending on the details of the accident. Special audits check the status of on-site investigations to determine the cause of the accidents, the progress of recurrence prevention measures, and whether or not there are any points for improvement.
State of Occurrence of Occupational Accidents
In 2023 (January-December), there were no occupational accidents resulting in the death of an employee or contractor employee. (There have been no occupational accidents resulting in the death of an employee, including contractor employees, over the past six years.) The frequency rate for all occupational accidents in 2023 (January-December) was 1.09 (0.93 in Japan), meaning that we were not able to achieve our target of 1.0 or less.
Lost-time injury frequency rate and all occupational accident frequency rate
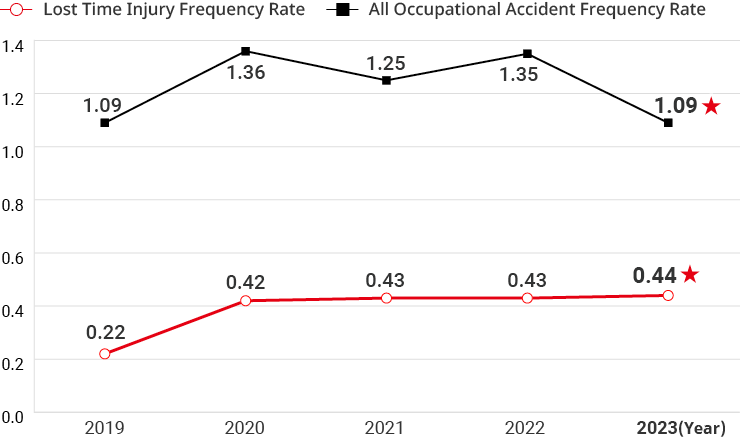
- *Lost-time injury frequency rate indicates number of lost-time injured persons per one million working hours (figures are calculated based on calendar years).
- *All occupational accident frequency rate indicates both lost-time injured persons and non-lost-time injured persons per one million working hours (figures are calculated based on calendar years). Includes full-time employees, fixed-term employees, part-time employees, and temporary employees. This rate has been assured independently since 2022.
- *Corrected the all occupational accident frequency rate for FY2021 in January 2024.