Composite Material
From Material Supplier to Tier 1 Supplier
Prior to 2017, Teijin supplied some low-volume carbon fiber reinforced plastic (CFRP) components to automakers. However, the company was primarily a material supplier - specifically carbon fiber - to Tier 1 suppliers. With the acquisition of Inapal Plastics (now Teijin Automotive Technologies Portugal, S.A.) and Benet Automotive (now Teijin Automotive Technologies Czech s.r.o.), Teijin established its position as a true Tier 1 supplier.
Currently, Teijin not only develop materials, but also involved in everything from the vehicle design to the mass production of prototypes and final vehicles.
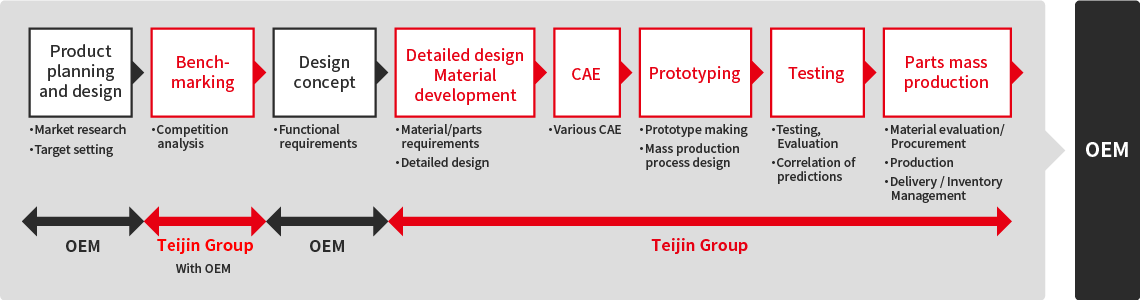
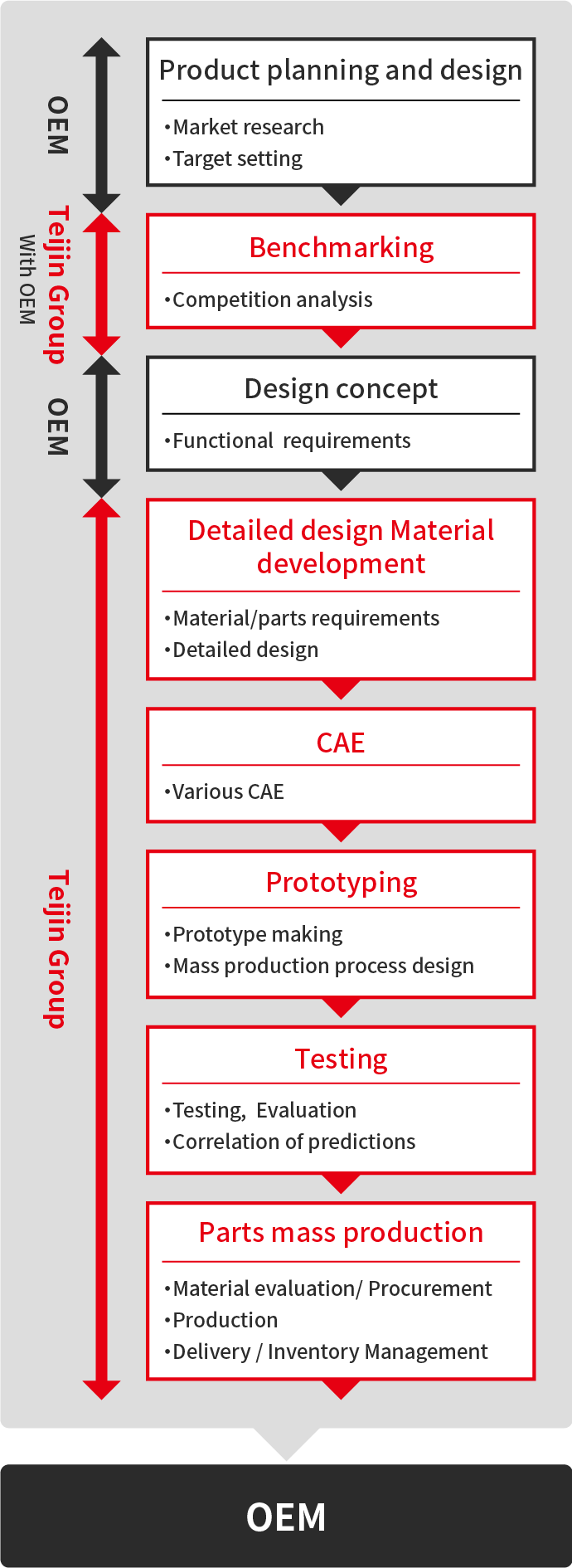
First Commercial Application of CFRTP
Teijin developed a proprietary, carbon fiber reinforced thermoplastic (CFRTP) material that is fully recyclable. Called Sereebo®, this material is being used by General Motors on the GMC Sierra for the pickup box. Compared to using steel, it is 40 percent lighter, offers 10 times greater impact resistance, is more corrosion-resistant. The molding time for Sereebo® is approximately one minute, having the high mass productivity required for automotive parts. This is the world's first use of CFRTP for structural parts in a high-volume production vehicle.
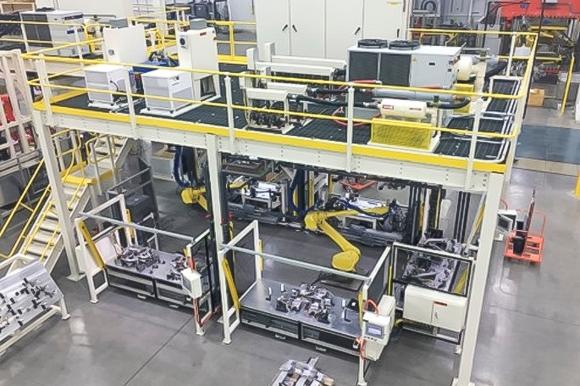
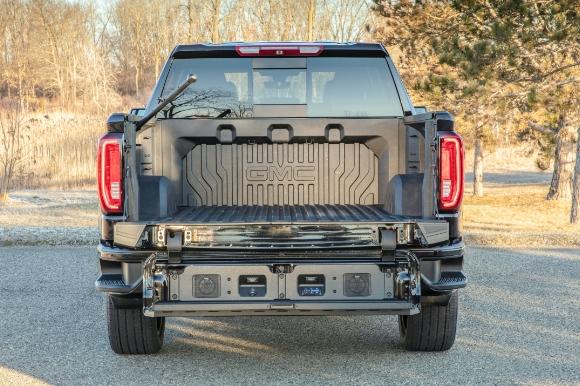
Multi-Material Battery Box for EVs
To achieve Carbon Neutral in the future, the automotive industry is actively working to convert their offerings from ICE vehicles to electric vehicles. While many OEMs are currently using our composite battery covers, we are offering a full battery enclosure that includes a composite tray and cover, and a metal frame. The cover and tray are made of our proprietary flame-retardant sheet molding compound (SMC), and the frame is made of metal. The optimal structural design ensures both weight reduction and safety.
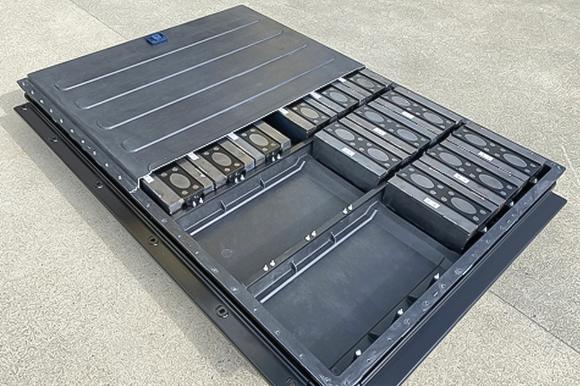
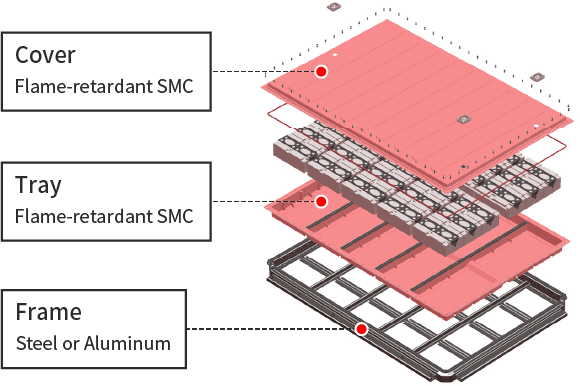
Flame Retardancy Test for SMC
The "GB standard" for flame retardancy is one of the most stringent global standards that battery enclosure must meet. This standard stipulates a very rigorous test that the flame does not penetrate the battery cover and reach the vehicle occupant space within 5 minutes after the start of combustion, allowing passengers time to escape from the vehicle in the event f a fire.
Teijin's flame-retardant SMC been confirmed to not penetrate even in a 10-minute flame exposure test equivalent to UL94-5VA.
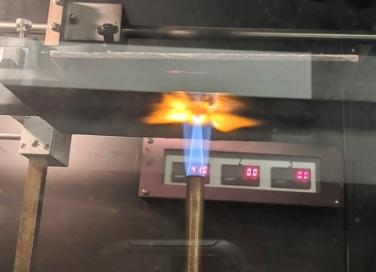
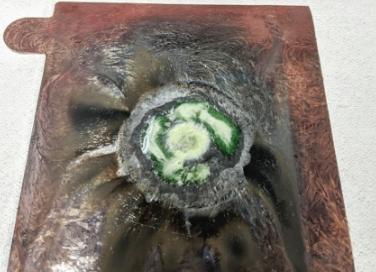
<Test condition>
-
UL94-5VA equivalent test (@ t2.0mm)
Flame temperature:700℃-1200℃
- 10-minute flame exposure
- Performance evaluation by watertight test and cross-section observation
Reducing Our Environmental Impact
As regulations to reduce global warming and protect the environment become stricter, and CO2 emissions reduction targets more stringent, Teijin is actively working to reduce its environmental impact. In addition to reducing the weight of automotive components, we are working to reduce the impact on the environment by reducing CO2 emissions during the entire component life cycle - from production to disposal.
For example, Sereebo® uses carbon fiber, and CO2 emissions from raw materials account for 70%. However, since Teijin uses its own carbon fiber, it has the advantage of being able to reduce CO2 derived from carbon fiber in-house. There are several approaches to reducing CO2 emissions associated with Sereebo®. By reducing and recycling scrap in the process, and using renewable energy and bio-derived resins, it is expected that CO2 emissions will be reduced by 76% in total compared to the present.
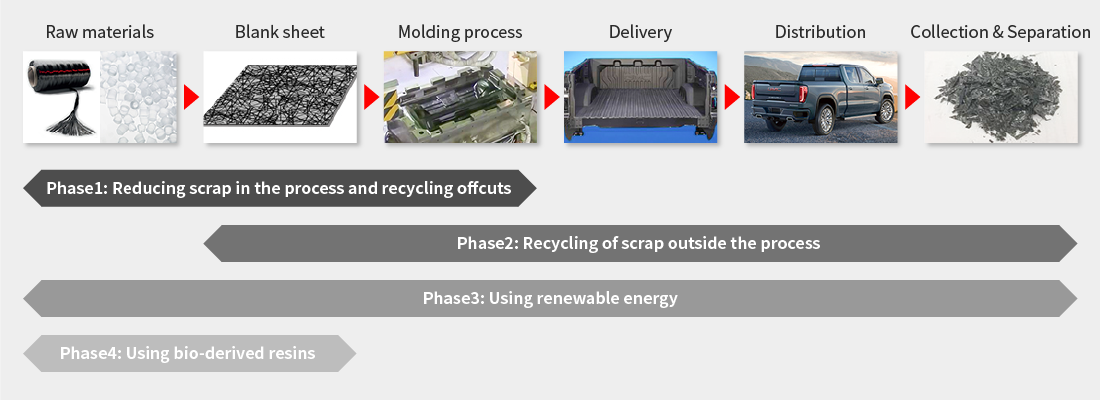
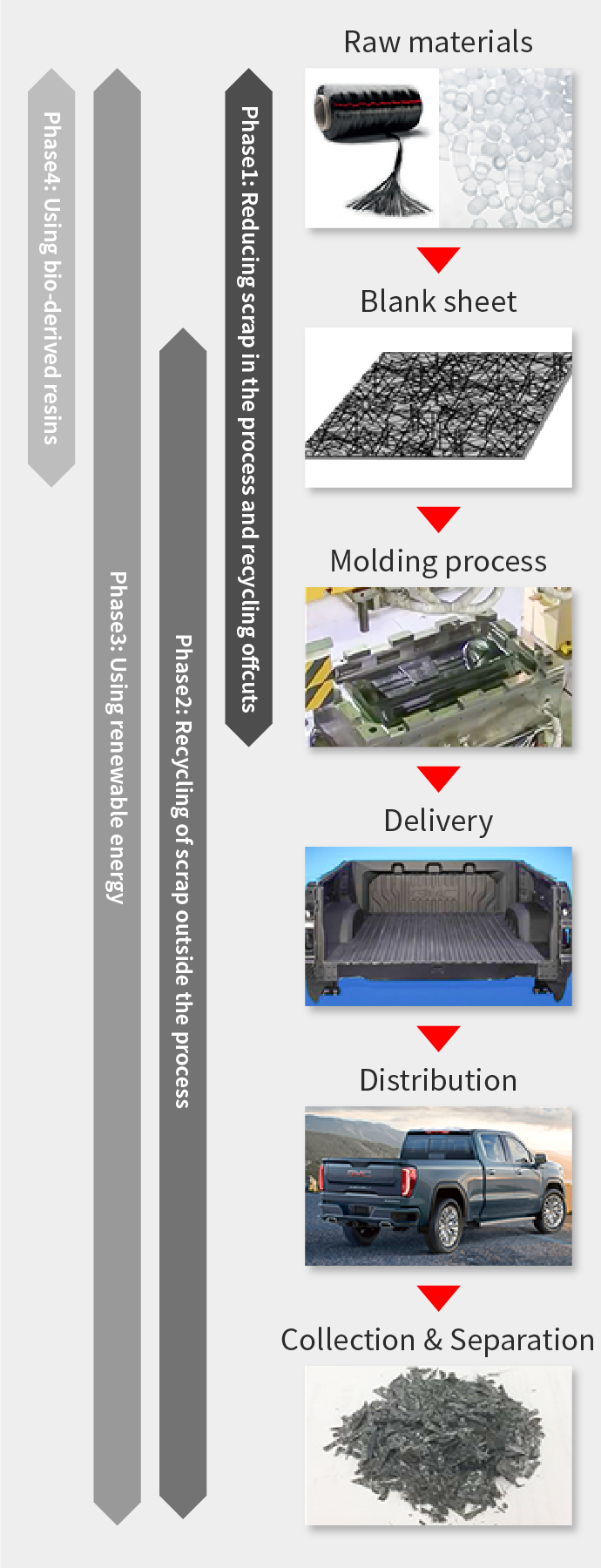
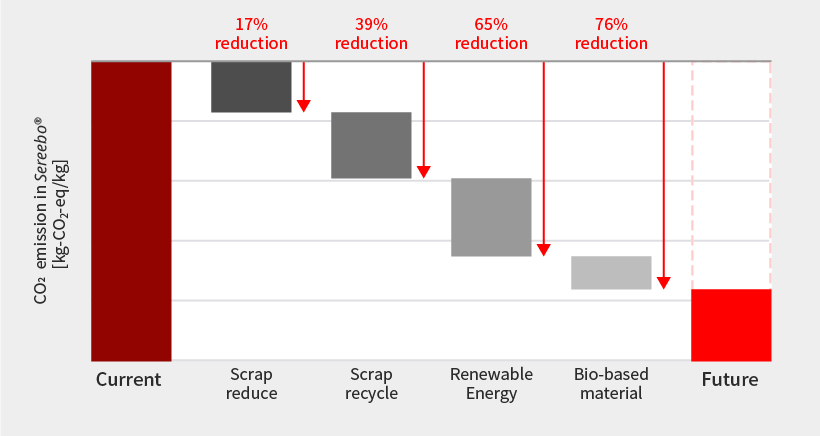
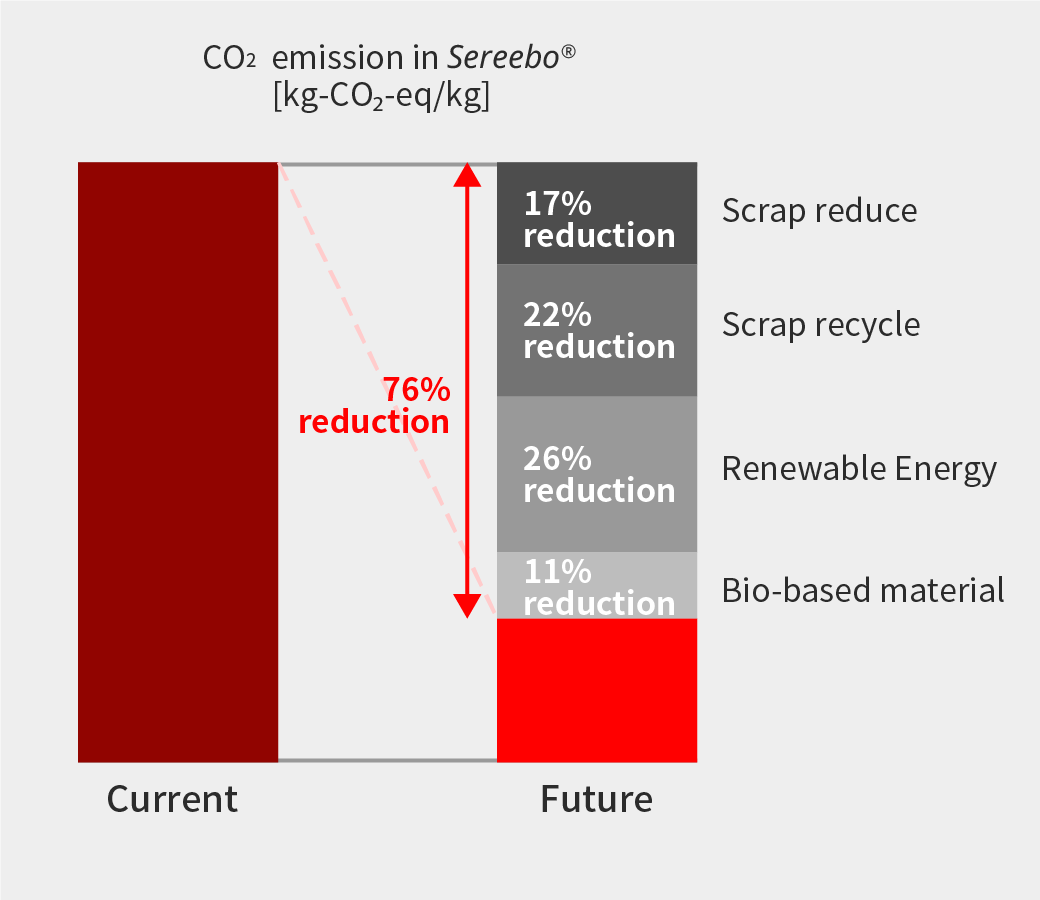